EVENT
Automotive Innovation Forum 2025
Join us in Darmstadt on May 13 & 14 at the spatial computing booth - book a meeting with us today!
LIVE SHOW
Hololight Celebrates 10 Years of XR Innovation
Join our Live Show on LinkedIn on May 22nd
ABOUT US
Explore Hololight's XR Solutions
We are a deep tech company and deliver the most powerful XR steaming solution
PRESS RELEASE
Hololight Becomes a Member of the Khronos Group
By joining this global consortium, we are committed to actively contributing to the OpenXR standard
VIDEOS
Hololight Showcase
Learn More about our Products from our Extensive Video Library
PRESS RELEASE
Hololight Celebrates 10 Years of XR Innovation
Pioneering the Future of Augmented and Virtual Reality Since 2015
TRUSTED BY INDUSTRY LEADERS
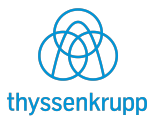
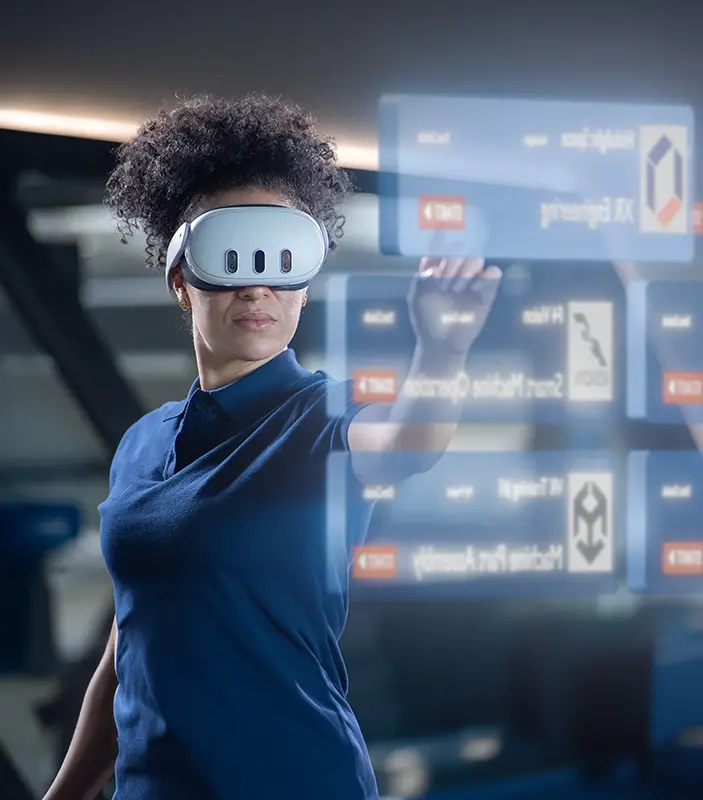
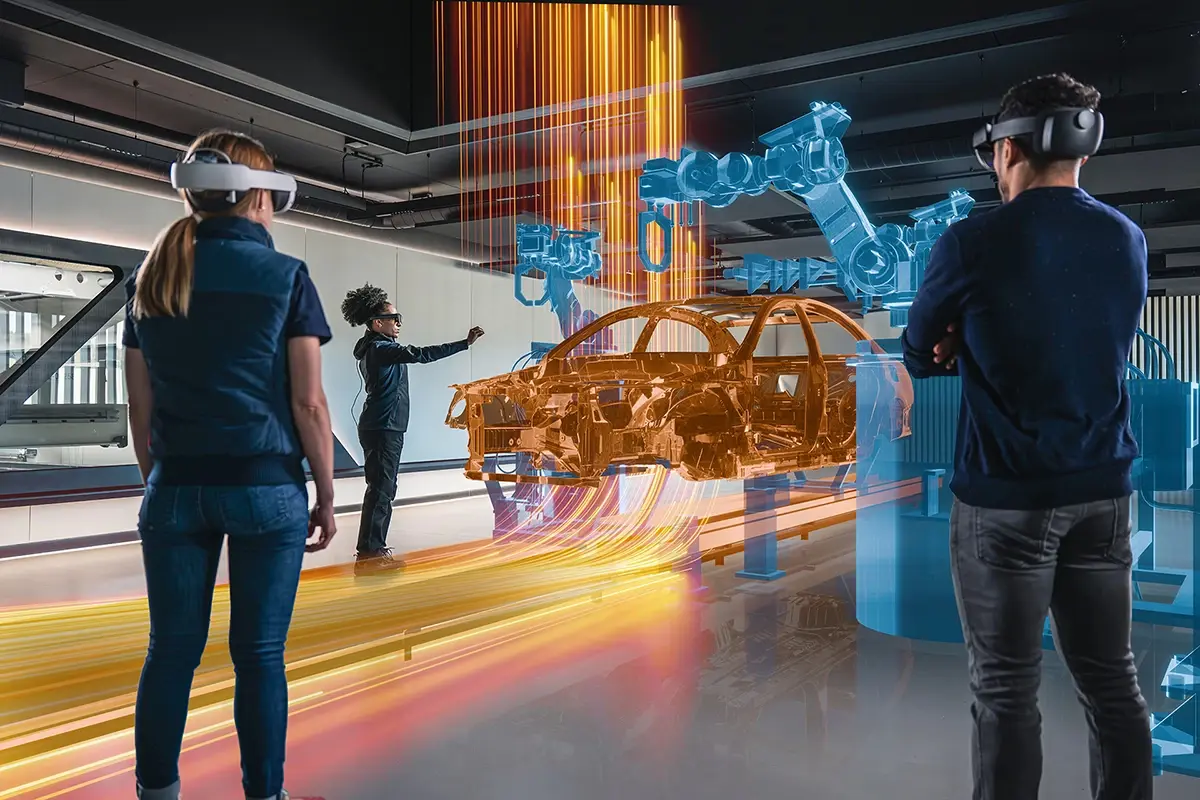
XR Engineering Software
3D CAD Visualization in XR for
Design & Engineering
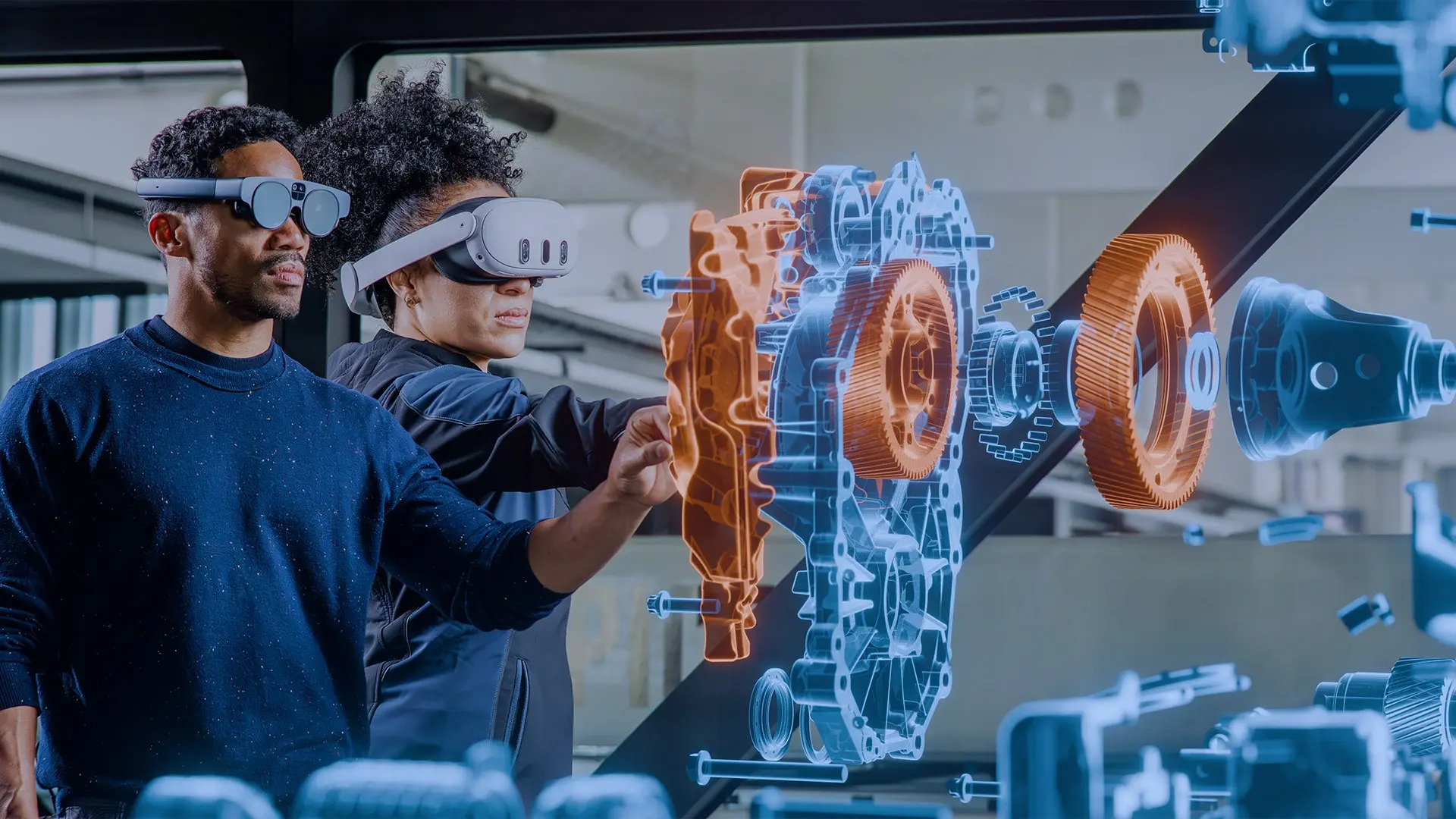
OUR PRODUCTS
Powered by Hololight's XR Pixel Streaming Technology
XR Engineering Software
3D CAD Visualization in XR for
Design & Engineering
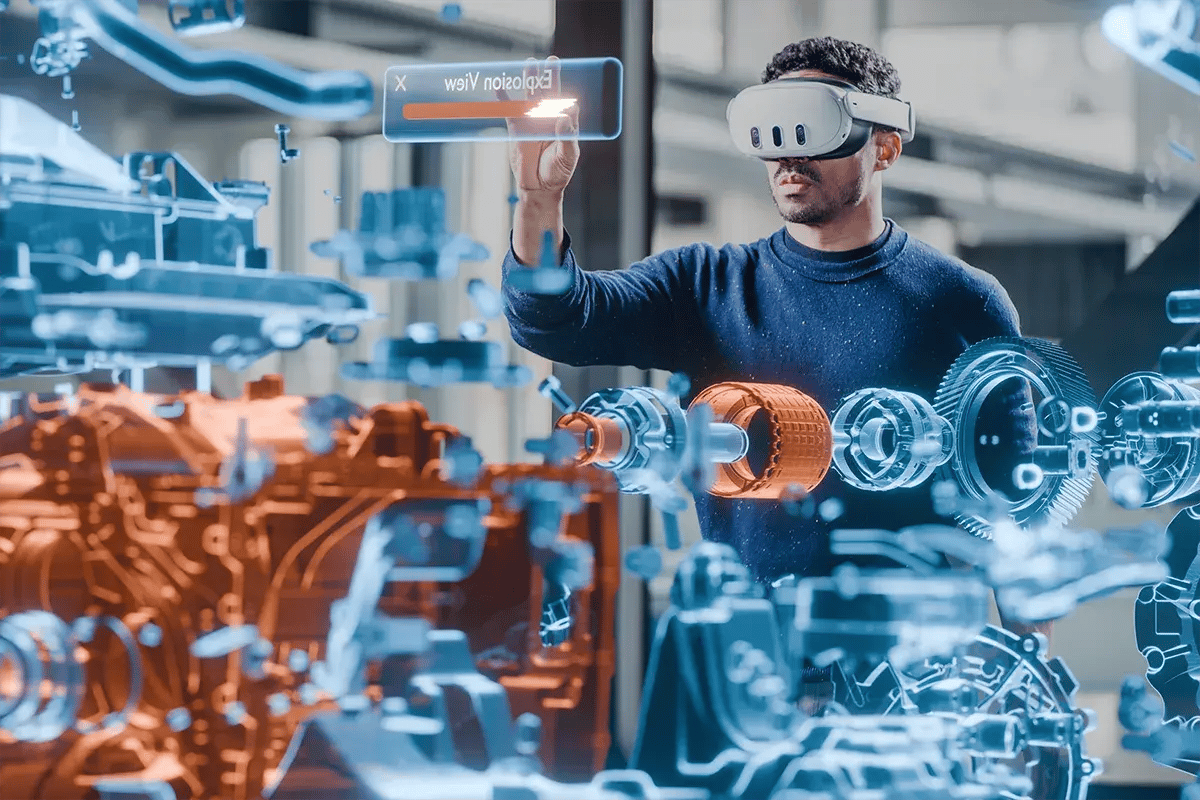
XR Engineering Software
3D CAD Visualization in XR for
Design & Engineering
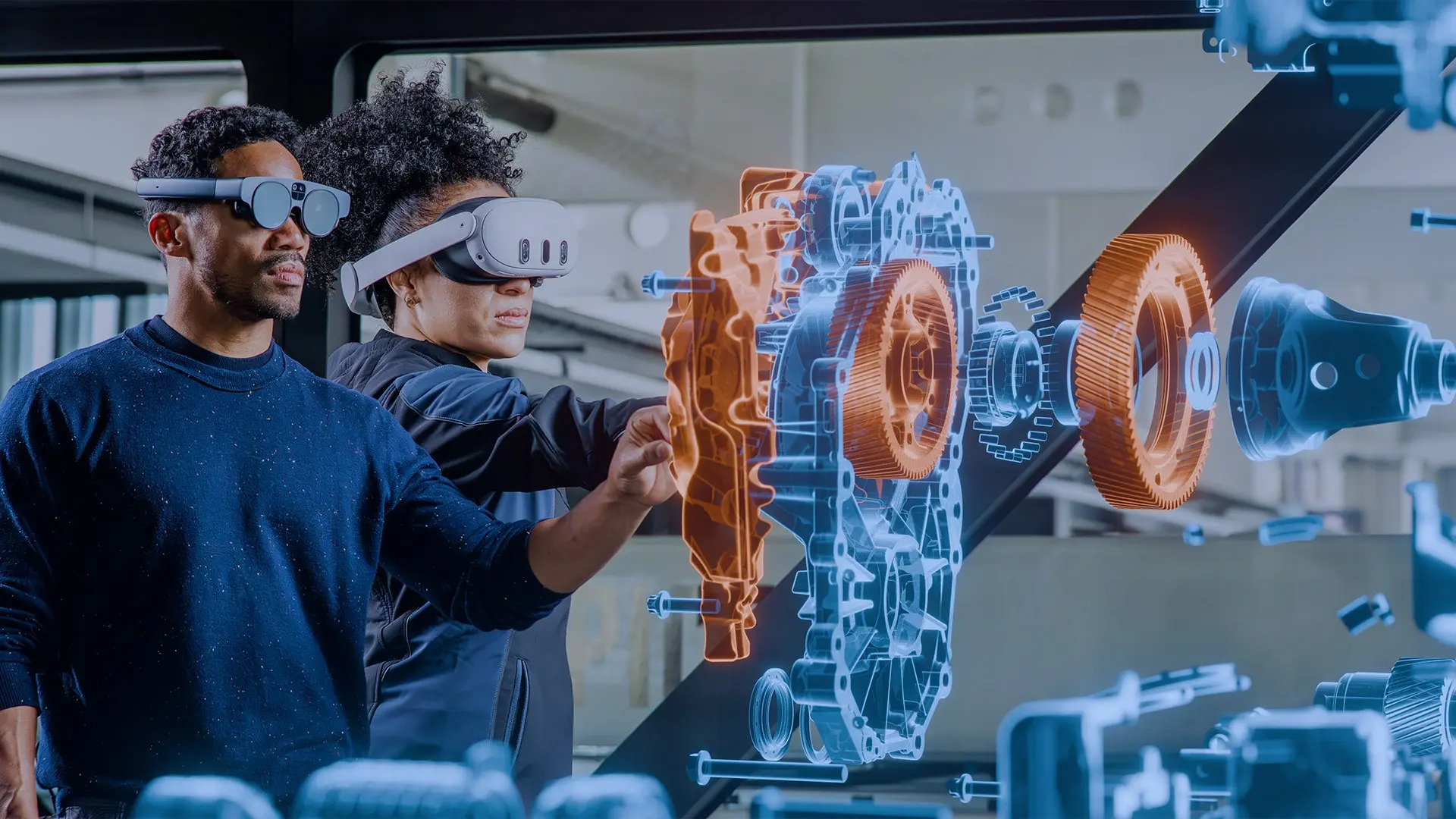
XR Engineering Software
3D CAD Visualization in XR for
Design & Engineering
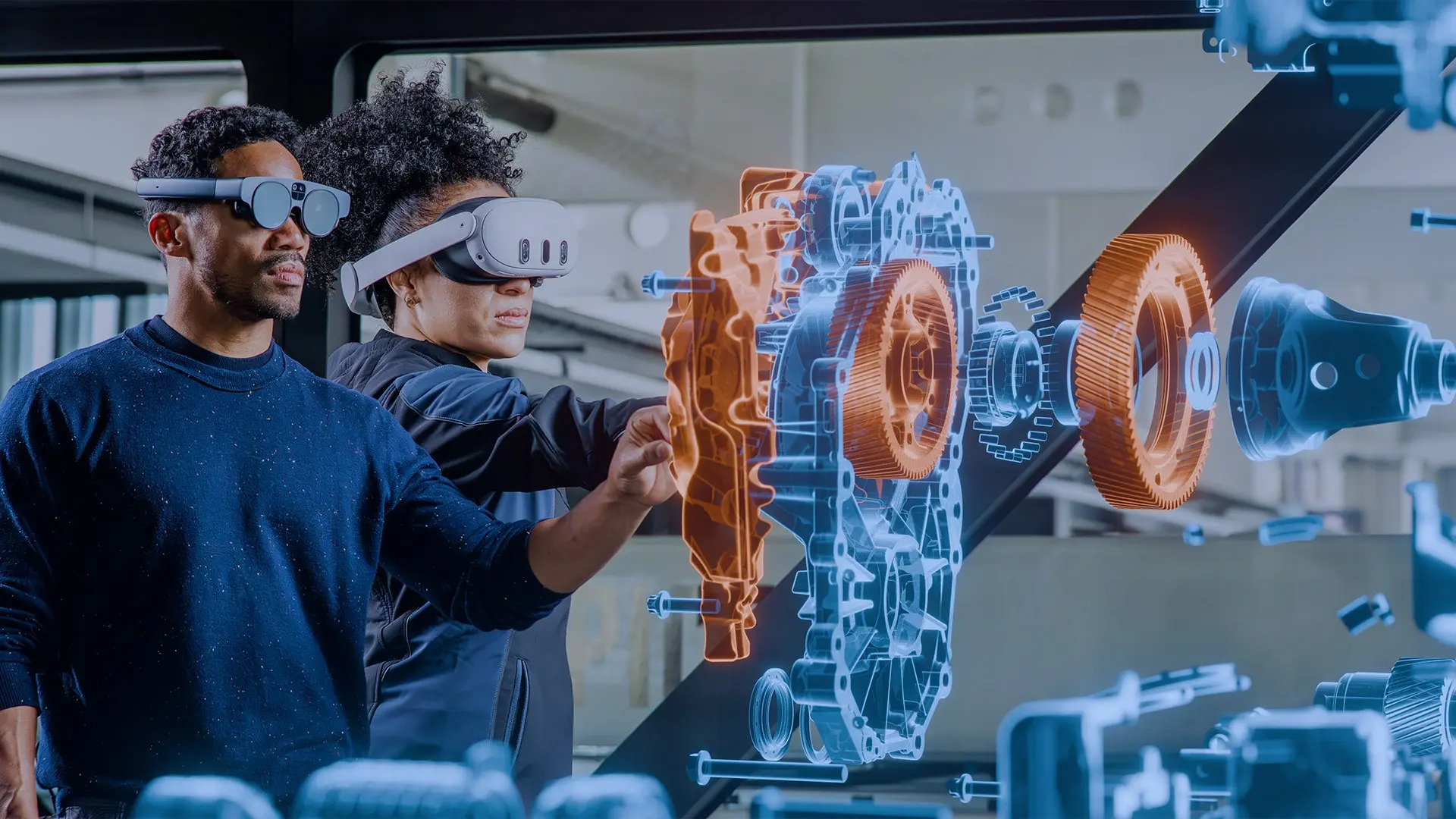
XR Engineering Software
3D CAD Visualization in XR for
Design & Engineering
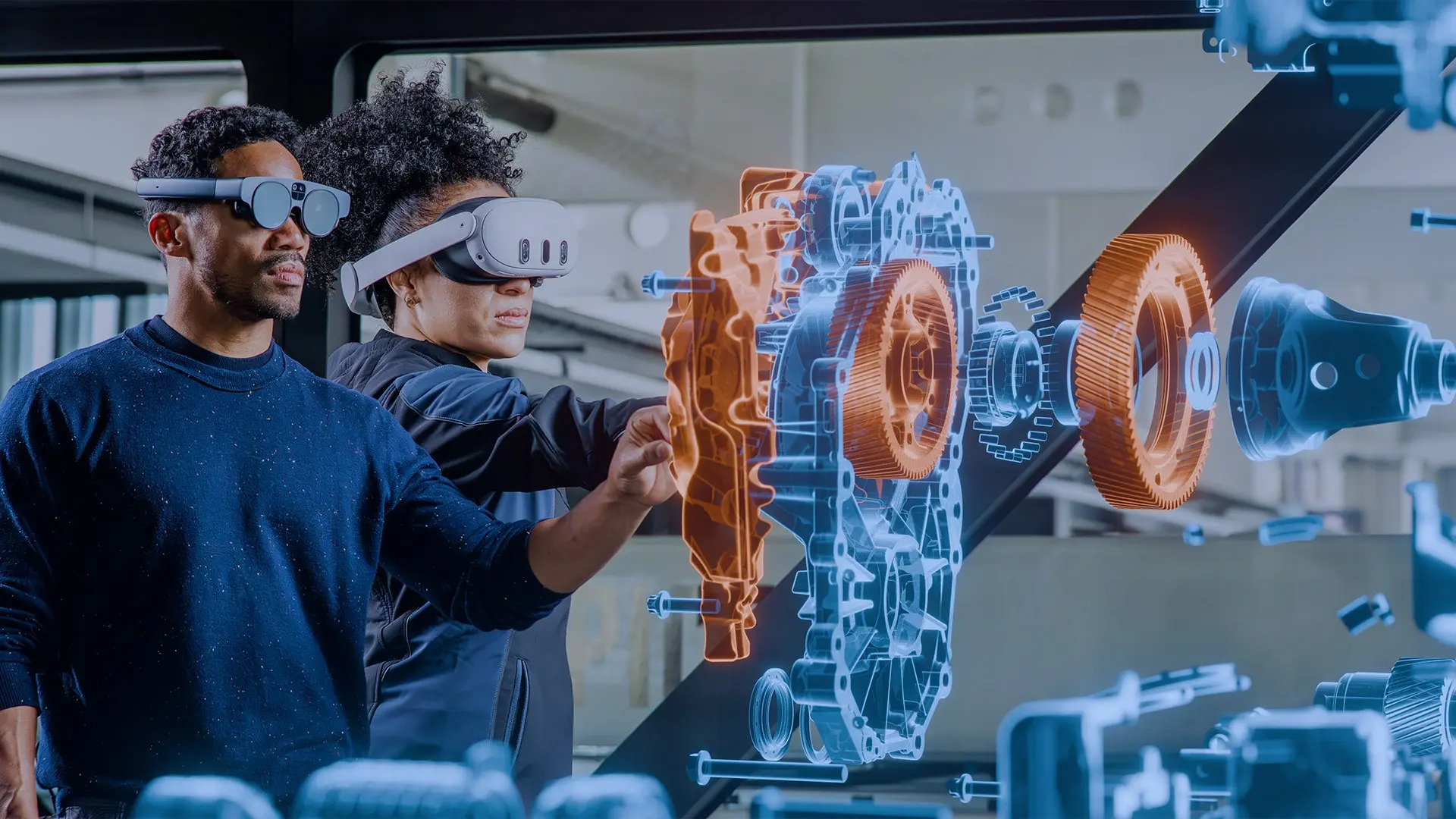
We have many different use cases with XR. For us it's building the foundation of tools we can use to utilize XR across the enterprise. It opens a lot to be able to stream multiple applications from a platform like Hololight Hub.
We have many different use cases with XR. For us it's building the foundation of tools we can use to utilize XR across the enterprise. It opens a lot to be able to stream multiple applications from a platform like Hololight Hub.
We have many different use cases with XR. For us it's building the foundation of tools we can use to utilize XR across the enterprise. It opens a lot to be able to stream multiple applications from a platform like Hololight Hub.
TESTIMONIALS
Leading Companies Trust Hololight
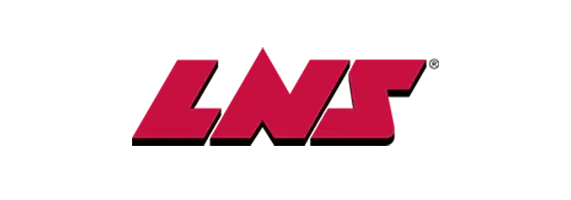
The ease of use and the return on investment is exactly what we were looking for. It’s as easy as switching on a computer. For us, now it’s second nature to use Hololight.
– Jamie Towers | Chief Technical Officer
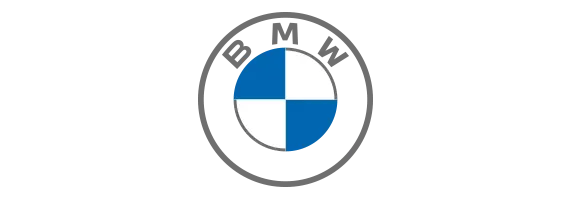
With AR glasses and CAD data, we can find out much more quickly if the production worker will be able to fit the part correctly later in production. As a result, we need far fewer test setups.
– Michael Schneider | Head of Complete Vehicle
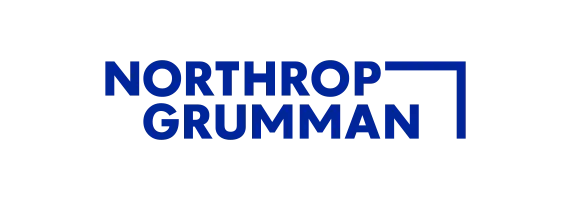
We have many different use cases with XR. For us it’s building the foundation of tools we can use to utilize XR across the enterprise. It opens a lot to be able to stream multiple applications from a platform like Hololight Hub.
– Michael Hinckley | Sector Manager Manufacturing Systems Engineering
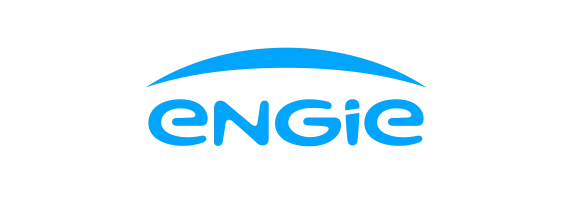
The cooperation with Hololight is always constructive, friendly, and goal-oriented. My ideas are well received, and the team considers and implements them according to our individual requirements.
– Jörn Stiegelmeier | Head of Technology & Development
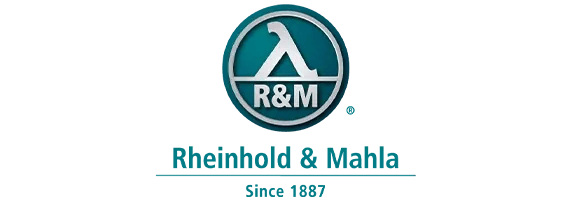
By using Augmented Reality, we avoid creating unnecessary prototypes and therefore have to make fewer revisions. It has also helped us tremendously with cross-cultural communication and allowed us to make decisions faster.
– Dr. Calvin Brett | Director of IT & Digitalization
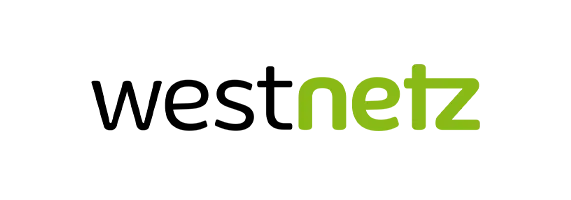
The project with Hololight has shown us how Augmented Reality helps to take workflows and learning processes to a new level of efficiency.
– Deliah Hecker | Digitalization, Innovation and Technology Division
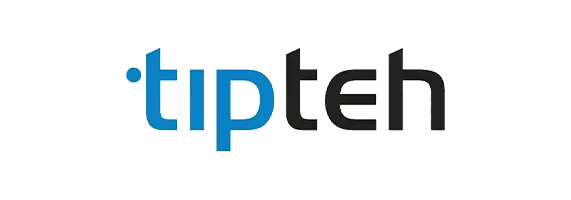
My recommendation to everyone is to try it out and see how Augmented Reality and especially the Hololight Space Software is a total game changer for engineering.
– Mileta Vracar | Development Manager Engineering
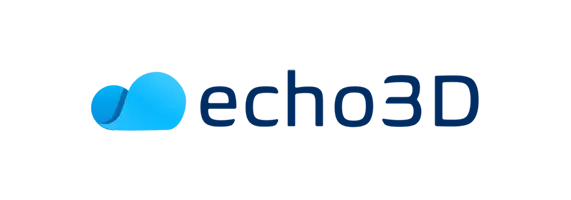
By harnessing the power of XR Streaming, we've been able to deliver a more immersive end-user experience to customers in need of AR training solutions. It's not just about reimagining what's possible - it's about making it a reality.
– Alon Grinshpoon | CEO
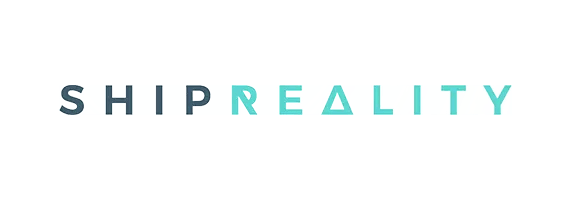
Hololight Stream has amazing potential for AR/VR visualization of massive digital twins and real-time monitoring of projected complex 3D designs merged with as-built environments in shipping and other industries.
– Georgios Bourtzos | CEO and Co-Founder
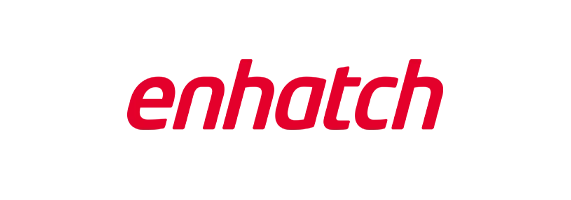
With Hololight Stream, we save time and money processing data by just avoiding converting volumes of data from one syntax to another. We can simply keep the high-resolution data from the iPad or computer and stream it to the AR headset.
– Peter Verrillo | (former) Co-founder and CEO
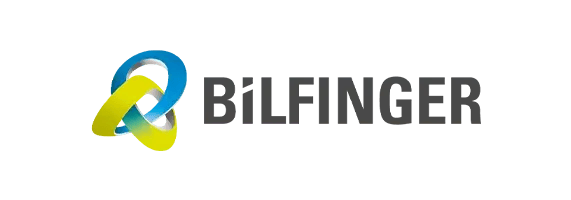
By visualizing true-to-scale 3D models in the actual plant as holograms, we can provide all stakeholders with a better understanding of the plant before it is constructed, while also creating a real wow effect.
– Tobias Bauchrowitz | Head of Engineering
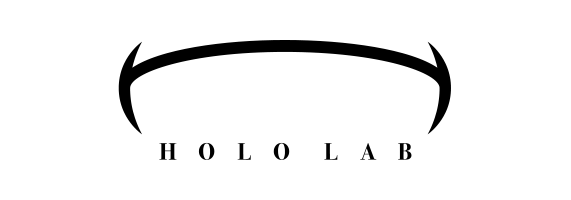
Before integrating the XR streaming solution Hololight Stream, we needed to align customer needs to the performance limitations of mobile computing devices. Implementing Hololight Stream in Unity is extremely simple. It took us less than 20 minutes.
– Takesen – Takehisa Ito | Co-Founder and COO
CONTACT
Book a Meeting
Europe
North America